Cabin stowage systems have a critical impact on aircraft functionality and efficiency. These systems significantly influence the passenger experience, cabin crew productivity, and an airline’s overall operational performance. Therefore, airlines should carefully consider their selection of stowage systems to achieve maximum utility from the scarce available space.
Selecting individual stowage solutions, in isolation, to meet specific needs can lead to a disjointed, inefficient system that fails to address the overall operational requirements of the airline. The lack of coherence in the system can lead to storage inefficiencies, wasted space, and increased operational costs.
This is where the integrated approach comes into play. Rather than separately addressing individual storage needs, an integrated approach to airline stowage systems considers the entire aircraft’s stowage requirements. Each component needs to be selected to ensure it is the most suitable option available on the market today for the functions it will serve, but consideration also needs to be given to the location and distribution of all components of the overall stowage system. This approach ensures that every part of the stowage system works in harmony, optimising space utilisation, improving operational efficiency, and enhancing passenger satisfaction.
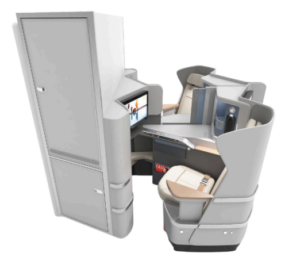
One of the primary advantages of an integrated approach is the streamlined and efficient utilisation of cabin space. By considering the complete stowage needs of an airplane, from the passenger cabin to the cockpit and the galley, an integrated approach can optimise the layout for maximum storage capacity, locating each component where it is more useful for its intended purpose and best facilitates the efficient flow of passengers and crew.
An integrated approach to stowage system design thereby enhances the passenger experience by providing more comfortable and accessible stowage solutions. By optimising the design of stowage systems, airlines can provide passengers with easy access to their personal items and more space for comfort during the flight, enhancing their overall flying experience.
Operational efficiency
Weight reduction is a top priority for airlines, both now and in the future. The aviation industry meticulously examines every aspect of an aircraft to reduce weight and improve efficiency. This pursuit is driven not only by the direct financial benefits of reduced fuel consumption, but also by the industry’s commitment to achieving net-zero goals.
As a result, weight plays a crucial role in the selection of closets and other stowage components in the aircraft cabin. These components must be lightweight yet structurally strong enough to withstand constant use and the safety challenges posed by turbulence and potential crashes.
An efficient stowage system also contributes to operational efficiency by reducing the turnaround time between flights. It accomplishes this by improving the flow of passengers and crew during the boarding and deplaning processes. This not only enhances overall productivity, but also improves the travel experience for everyone involved, reducing stress and potential conflicts, and enhancing the airline brand.
Easier cleaning and maintenance of well-designed stowage systems can also lower maintenance costs and reduce aircraft turnaround time.
Innovative stowage components
Stowage components range from large monuments for the storage of large items, to compact slider panels tucked behind seats for emergency equipment. Aircraft stowage monuments come in a variety of types, each of which can be tailored to meet the specific needs of the routes the aircraft will serve.
Monument stowages
Monuments are suitable for storing a wide variety of items, from coats and baggage, to wheelchairs and galley carts.
To maximise space utilisation, front-row monuments (FRM) for business-class cabins can be seamlessly integrated with seating and other interior elements with minimal gaps.
Under-bin closets
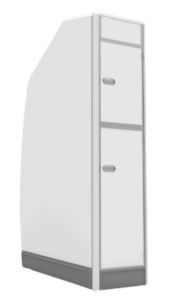
In the main cabin, under-bin closets can provide significant stowage space and can be customised for a wide variety of uses to support everything from emergency equipment to miscellaneous stowage. Double doors provide easy access and allow for the storage of large objects. Upper and lower coat rods increase storage density. These closets are often placed in prominent locations within the cabin, and therefore a quality appearance and customiaed logo/branding are critical. Provisions can also be provided on the forward or aft face, such as literature pockets, LCD monitors, seat power boxes, and baby bassinets.
Video control centres
To improve in-flight service and situational awareness, the Video Control Center (VCC) in an aircraft cabin assists the crew with several tasks and allows the airline to provide clients with new services. Electrical provisions can be provided on a VCC to support the airline’s specific needs, such as a display docking station, crew terminal, handset INSTL, remote modem unit, switch panel, seat power box, system control unit, removable box, and Wi-Fi placard holder.
Doghouses and slider panels
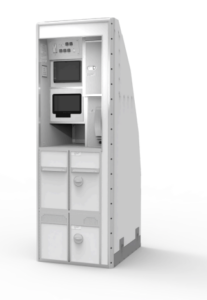
There are various ingenious storage solutions that can effectively utilise every inch of available space. This includes the area behind the last row of seats, adjacent to a divider or monument. Dividers, doghouses, and divider/doghouse combinations can be customised to support the airline’s needs with logo/branding and provisions such as LCD monitors, coat hooks, and literature pockets.
Slider panels offer a highly efficient solution for storing emergency equipment in tight spaces. The airline typically customises the provision of emergency equipment based on its specific requirements. It is crucial for the sliding mechanism to be sturdy and long-lasting, designed and tested to withstand both the weight and impact during emergency situations.
Collaborative design process
A highly collaborative design process that engages with airline clients right from the conceptual stage (as Jamco America does) is important. This approach involves key stakeholders in every step of the design and development process, ensuring that the final stowage solutions are not just innovative but also perfectly aligned with the specific operational needs and brand vision of each airline.
By fostering this level of collaboration, the team can ensure that each product is a true reflection of the airline’s identity, merging functionality with the unique aesthetic and practical requirements of clients.
Fully integrated aircraft interiors
For the same reasons that it makes sense to have a coherent plan that integrates all stowage components, it also makes sense to design and implement the stowage system in conjunction with a complete plan for the aircraft cabin interior, including seating, galleys, and lavatories.
Such an approach guarantees seamless integration between components, as well as a uniform look and feel. Furthermore, collaborating with an integrator, such as Jamco America, guarantees not only the seamless integration of all components, but also the smooth execution of the installation/retrofit process within budget and on schedule. This approach is superior to the alternative of involving multiple vendors for different components.
In conclusion, the adoption of an integrated approach to aircraft stowage systems significantly enhances the efficiency and functionality of aircraft interiors. This approach ensures a uniform aesthetic and streamlines the installation process.
About Jamco America
More than 20 major airlines have turned to Jamco America for turnkey aircraft interior integration programmes. The company delivers complete aircraft interior solutions from its Everett, WA facility, integrating fully staffed engineering, technical publications, manufacturing teams, as well as testing capabilities (electrical, dynamic, thermal, acoustic, life cycle, and material strength) and an on-site Federal Aviation Authority Organization Designation Authorization (FAA ODA) certification department.
Edward Pauly is senior product manager and sales manager at Jamco America.